How do They Make Gears? - Gear Forging Process Detailed Introduction
2020-02-21 15:47:11Gear forging processes include blank forging, normalizing, turning machining, hobbing on shaper machine, gear shaving, heating treatment, grinding machining. Following shows the detailed introduction of each forging process.
Gear Forging Process Introduction
Blank forging
Hot closed die forging is also the main blank forging process of auto gear forgings. In recent years, the technology of cross wedge rolling machine has been widely used in shaft and gear parts process. This kind of technology is suitable for blank forging of complex stepped shaft. It has not only high precision, small machining allowance, but also high production efficiency.
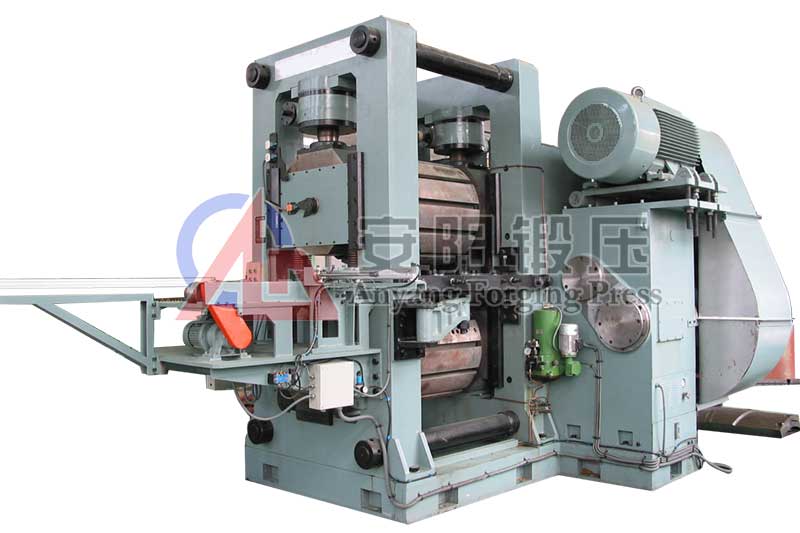
Normalizing
The purpose of this process is to obtain the hardness suitable for subsequent gear cutting and to prepare the structure for the final heat treatment, so as to effectively reduce the heat treatment deformation. The material of gear steel used is usually 20CrMnTi, and the normal normalizing is greatly affected by personnel, equipment and environment, it makes it difficult to control the cooling speed and uniformity of the workpiece, resulting in large hardness dispersion and uneven microstructure, which directly affects the metal cutting and final heat treatment, making the thermal deformation large and irregular, and the quality of the parts can not be controlled. Therefore, the isothermal normalizing process is adopted. The practice shows that the use of isothermal normalizing effectively changes the disadvantages of general normalizing, and the product quality is stable and reliable.
Turning machining
In order to meet the positioning requirements of high-precision gear processing, CNC lathe is used for the processing of gear blank, and the machining of hole diameter, end face and outer diameter under one clamping is completed synchronously by using mechanical clamping without regrinding turning tool. It not only ensures the perpendicularity requirements of the inner hole and the end face, but also ensures the small size dispersion in the production of large batch of gear blanks. In addition, the high efficiency of CNC lathe processing also greatly reduces the number of equipment, good economy.
Hobbing and gear shaping
A large number of gear hobbing machines and gear shapers are still used in the processing of gear parts. Although it is convenient to adjust and maintain, the production efficiency is relatively low. If a large production capacity is completed, multiple machines are required to produce at the same time. With the development of coating technology, the re coating of hob and insert blade after grinding is very convenient. After coating, the service life of the tool can be significantly improved, which can generally be increased by more than 90%, effectively reducing the number of tool changes and grinding time, with significant benefits.
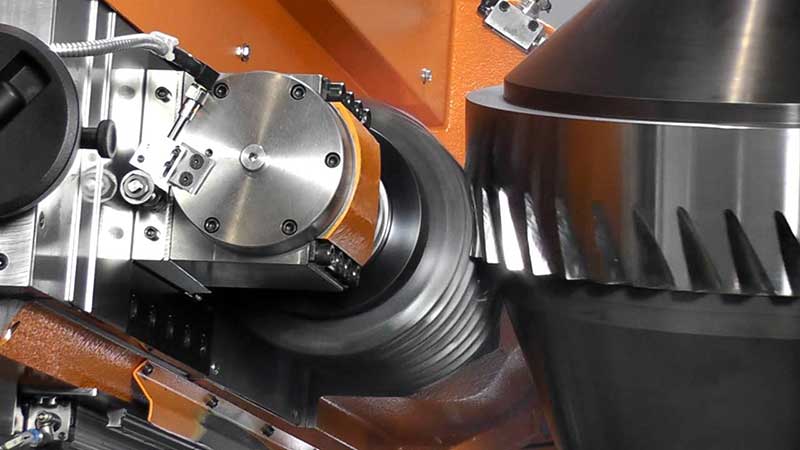
Gear shaving
Radial shaving technology is widely used in the production of automobile gears with its advantages of high efficiency, easy realization of the requirements of tooth shape design and tooth direction modification.
Heat treatment
Carburizing and quenching are required for automobile gears to ensure their good mechanical properties. Stable and reliable heat treatment equipment is essential for the products that will not be grinded after heat treatment.
Grinding machining
It is mainly to finish the inner hole, end face and outer diameter of the shaft of the gear after heat treatment, so as to improve the dimensional accuracy and reduce the geometrical tolerance.